5 Ways Faulty Welds Affect Newport News Shipyard Safety
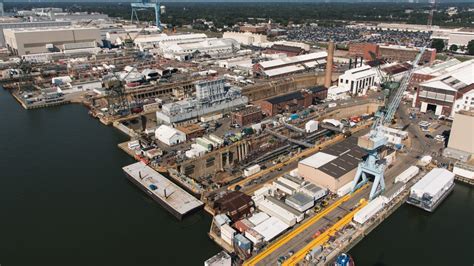
Understanding the Impact of Faulty Welds on Shipyard Safety

Newport News Shipyard, one of the largest and most renowned shipyards in the world, prioritizes safety above all else. With a workforce of over 25,000 employees, ensuring the safety of each and every individual is a monumental task. One critical aspect of shipyard safety is the quality of welds. Faulty welds can have severe consequences, affecting not only the structural integrity of the ships but also the well-being of the workers. In this article, we will explore five ways faulty welds can impact Newport News Shipyard safety.
1. Reduced Structural Integrity

Welds play a crucial role in maintaining the structural integrity of ships. A faulty weld can compromise the overall strength of the vessel, making it more susceptible to damage or even catastrophic failure. This can have disastrous consequences, especially in harsh marine environments where ships are exposed to extreme weather conditions, rough seas, and corrosive elements.
Key Statistics:
- A study by the American Society of Mechanical Engineers (ASME) found that welding defects are responsible for up to 50% of all structural failures in ships.
- The U.S. Coast Guard reports that weld-related defects are a leading cause of shipboard fires and explosions.
2. Increased Risk of Accidents and Injuries

Faulty welds can also increase the risk of accidents and injuries in the shipyard. When a weld fails, it can lead to a chain reaction of events, resulting in damage to surrounding equipment, structures, and even injuries to nearby workers.
- According to the Occupational Safety and Health Administration (OSHA), welding accidents are responsible for an estimated 4,000 to 6,000 injuries and fatalities in the United States each year.
- A study by the National Institute for Occupational Safety and Health (NIOSH) found that welding-related injuries are more likely to occur in shipyards due to the presence of hazardous materials and confined spaces.
3. Equipment Damage and Downtime

Faulty welds can also lead to equipment damage and downtime, resulting in significant economic losses for the shipyard. When a weld fails, it can cause damage to surrounding equipment, requiring costly repairs and maintenance.
- A study by the Society of Naval Architects and Marine Engineers (SNAME) found that equipment downtime due to weld-related defects can result in losses of up to $100,000 per day.
- The shipyard’s reputation and customer satisfaction can also suffer due to delays and equipment failures.
4. Environmental Hazards

Faulty welds can also pose environmental hazards, particularly in the event of a spill or leak. When a weld fails, it can release hazardous materials into the environment, contaminating soil, water, and air.
- The Environmental Protection Agency (EPA) reports that shipyard-related pollution is a significant concern, with welding and cutting operations contributing to air and water pollution.
- The shipyard’s environmental reputation and compliance with regulations can suffer due to faulty welds.
5. Decreased Employee Morale and Productivity

Finally, faulty welds can also affect employee morale and productivity. When workers are aware of potential safety hazards and equipment failures, it can lead to decreased job satisfaction and motivation.
- A study by the American Welding Society (AWS) found that welders who are concerned about safety and equipment reliability are more likely to experience decreased productivity and job satisfaction.
- Employee turnover and recruitment costs can also increase due to decreased morale and productivity.
💡 Note: The shipyard's safety culture and employee training programs can play a significant role in preventing faulty welds and ensuring a safe working environment.
In conclusion, faulty welds can have far-reaching consequences for Newport News Shipyard safety, affecting not only the structural integrity of ships but also employee well-being, equipment reliability, and environmental sustainability. By prioritizing weld quality and safety, the shipyard can minimize the risks associated with faulty welds and ensure a safer, more productive working environment.
What are the most common causes of faulty welds in shipyards?

+
The most common causes of faulty welds in shipyards include inadequate training, poor equipment maintenance, and insufficient quality control measures.
How can shipyards prevent faulty welds and ensure a safe working environment?

+
Shipyards can prevent faulty welds by implementing rigorous quality control measures, providing regular training and certification programs for welders, and maintaining equipment in good working condition.
What are the economic costs of faulty welds in shipyards?

+
The economic costs of faulty welds in shipyards can be significant, resulting in losses of up to $100,000 per day due to equipment downtime, repairs, and maintenance.
Related Terms:
- faulty welds shipyard newport news